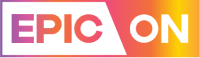
Lingang, China. Home to one of the largest and most modern excavator factory in the world 1000 square meters of production area, equipped with hightech machines of the latest generation. By this means Chinas market leader Sany wants to become the number one in the worldFor half a billion euros, the construction machinery giant has built the mega factory. Now 1,600 specialists ensure a breathtaking output: theoretically every ten minutes a new excavator can roll off the production line In order to achieve the enormous number of strokes, the huge production halls are equipped with the latest generation of robots. They process up to 250 tons of steel every day. In some areas the robots have completely taken over the production of the excavators. In the stateoftheart welding plant, for example, twentyfour workers were replaced by thirtytwo robots. They do the work in half the time. And this is not the only advantage: they are more precise, safer and much more costeffective in the longrun.Sanys topseller in the midrange class: the excavator SY215. Its price: one hundred and ten thousand euros. This makes it cheaper than any competitor model from Europe or United States. Its most spectacular feature: a blackbox that sends all of the recorded vehicledata to the control centre in China. In realtime. The Chinese produce the twentythree ton monster in just twentyfour working hours. The specialists have to work under extreme time pressure. This is also the case at the socalled marriage section where the heavily swaying, twelvetonne upper part has to be moved with millimetre precision onto the narrow slewing ring. The specialists also have only ten minutes at this station. So that Sany can deliver excavators at record speed on the way to becoming the world market leader.
It is the largest manufacturer of fire trucks in the world: Pierce Manufacturing in Wisconsin, USA. 1400 trucks are being built here every year – and each truck is one of a kind. Customers determine every detail from the first sketch on the 3D model to the finished truck. More than 13,000 individual components most of them laboriously crafted by hand are turned into an absolutely individual firefighting vehicle. Even the lettering and coats of arms so popular in North America are the result of Pierces manual work with brushes and genuine gold leaf. All this is only possible with a lot of experience. The three thousand employees have on average twelve years of professional experience. After all, not just any product is manufactured here, but in case of emergencies their quality is a matter of life and death. The demands placed on a fire fighting truck are correspondingly high: heavy as a truck, it must nevertheless be extremely manoeuvrable and fast. Take a megaframe, a cab equipped with lots of hightech, a highperformance water pump and a gigantic ladder: We accompany the production of a popular Enforcer fire truck from the very first step the construction of the chassis to the final acceptance by the customer. One of the highlights is the assembly of the TAK4 wheel axle. Developed in the military sector, it enables cornering at top speed without tipping over. After approximately three months of production, the grand finale is the installation of a gigantic 33meter turntable ladder on the roof of the Enforcer. A nervewracking task for the workers. Using two crane winches, they have to install the component, which weighs tons, with millimetre precision. No cable must be damaged. The final inspection shows whether the installation was successful. Then the customer receives his very own personal emergency vehicle.
It is the most renowned tyre manufacturer in the world: Pirelli. Their capacity: 75 million car tyres a year. 32,000 employees worldwide, including 1,400 engineers. The most prestigious car manufacturers in the world rely on their experience. We follow the production of the PZero, Pirellis flagship product. It takes: 100 constituent materials, fifteen manufacturing steps, and over 50 performance tests undertaken in hightech laboratories. All for achieving the best possible compromise between three irreconcilable and contradictory properties: low rolling resistance, strong grip and low wear. Only then will the P Zero, take to the streets of the world. In Settimo Torinese, Italy, the company manufactures its hightech tires on 200,000 square meters of floor space. Natural rubber is the basic raw material for around 130 years. But yet, a tire is so much more than simply rubber. The secrets of this Mega Manufacturing operation lie in the other ingredients too: A precisely measured blend of fillers, antioxidants, plasticizers, and curing agents. A car tire is a complex hightech product with many individual layers. Up to ten different rubber compounds are required for different zones of the tire. Together with textile fibers and steel wires. Only then tires are able to withstand extreme stresses. A new tyre is specially developed for each car brand. The PZeros development is based on the experience gathered in the Formula One World Championship, for which Pirelli is the sole supplier. We make a detour to the development and testing department at Pirellis headquarters in Milan and accompany a new PZero to the test track.
Trucks: Kings of the road with enormous power. Their manufacture demands a good eye, absolute precision and above all: perfect logistics. One of the worlds largest truck factories is located in Belgium, close to the romantic town of Ghent. Its the ideal location, close to thousands of customers across Western Europe. This is where Volvo produces its bestseller: the alltime allrounder FH one of the most popular trucks in Europe with the most powerful engines in the industry Approximately two hundred trucks each day Each one unique: every truck leaving this factory is different: Mega Manufacturing individually tailored to customer requirements in a feat of logistical perfection. Timed to the minute. Around one thousand five hundred individual parts are installed by the workers in two hundred and ten operations over eight hours from the simple unadorned chassis to a state of the art truck. This Mega Manufacturing takes huge amounts of energy. But suprisingly without CO2 emissions. Volvo Trucks in Belgium was the first carbonneutral car factory in the world. As early as 2009. Green energy, perfect logistics, a gigantic, fully automated warehouse, modern robots: the factory is still hightech. But nothing works here without welltrained people. Volvo Trucks calls themself a „people factory“. At the moment they are testing how to support their highlytrained workforces with new hightech equipment: exoskeletons and virtual reality glasses allow workers and computers to become one It could become the truck factory of the future
The Porsche Macan: the most successful horse in the stable of this legendary sports car manufacturer. A compact SUV, combining offroad qualities and everyday versatility with the DNA of a sports car. In its Leipzig factory Porsche produces with 4,300 employees over 90,000 Macan vehicles per year. Every single vehicle: absolutely individual and bespoke manufactured to order. A masterpiece of logistics and engineering design. Retaining their outstanding quality and delivering volume – a balancing act. Everything begins with the fabrication of the body. Eight hours is all they need for the entire production of a fully galvanized aluminumsteel car body. On more than 35 thousand square meters, a 400strong robot army supported by people turn pure sheet metal into subframes. Around the clock. A perfectly synchronized spectacle with the precision of a clockwork in perpetual motion. Each individual Macan car body is checked with utmost precision. The same applies to the paint surface and the assembled car. The extent of the individual quality control is unique in mass production – and for Porsche, an absolute necessity. Since the opening of the Leipzig factory, Porsche has invested over EUR 1.3 billion in this facility – and it is always constantly expanding. Protecting the environment is one key aspect of the investments. Energy is saved in the halls through efficient robotic use, and produced on the rooftops from natural solar energy. The photovoltaic system consists of more than 17,500 modules. Immediately behind the assembly halls and the companys own circular track, there is an entirely different world Here, Porsche has created ecological compensation areas for the sealed ground space. 25 Exmoor ponies and 75 aurochs graze on this managed ecosystem.
Hindi
Technology, Science
Marvin Entholt
Have a request or feedback? Click here